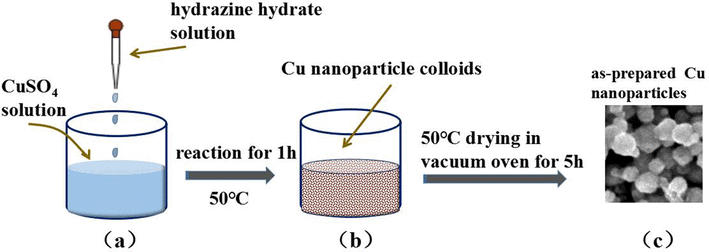
Ultra Fine Copper Powder is an essential material in various high-tech applications, such as electronics, catalysis, and advanced manufacturing. One of the most effective methods to produce high-purity Ultra Fine Copper Powder is through chemical reduction. This detailed blog post will delve into the chemical reduction process, its advantages, the specific steps involved, and its applications in increasing the purity of Ultra Fine Copper Powder.
Understanding Chemical Reduction
Chemical reduction is a process that converts copper ions in a solution into copper metal through a chemical reaction with a reducing agent. This method is highly valued for its ability to produce ultra-fine copper powders with exceptional purity and controlled particle sizes. The key to this process lies in the selection of appropriate reducing agents and precise control of reaction conditions.
Advantages of Chemical Reduction
- High Purity: Chemical reduction produces copper powder with high purity levels, often exceeding 99.9%. This is crucial for applications requiring minimal impurities, such as in electronics and conductive materials.
- Controlled Particle Size: The process allows for precise control over the particle size and distribution, essential for achieving specific physical and chemical properties in the final product.
- Uniformity: The powders produced through chemical reduction are typically uniform in shape and size, contributing to consistent performance in various applications.
- Scalability: This process can be scaled up to produce large quantities of ultra-fine copper powder, making it suitable for industrial applications.
The Chemical Reduction Process
The chemical reduction process for producing Ultra Fine Copper Powder involves several key steps, each critical to achieving the desired purity and particle characteristics.
1. Preparation of the Copper Salt Solution
The process begins with the preparation of an aqueous solution of a copper salt, commonly copper sulfate (CuSO₄). The concentration of the copper salt in the solution is carefully controlled to ensure optimal conditions for the reduction reaction.
2. Selection of Reducing Agent
Choosing the right reducing agent is crucial for the success of the chemical reduction process. Common reducing agents for copper powder production include:
- Hydrogen (H₂): Provides a clean reduction process without introducing impurities.
- Hydrazine (N₂H₄): Highly effective but requires careful handling due to its toxicity.
- Ascorbic Acid (C₆H₈O₆): A safer alternative, especially in laboratory settings.
3. Reduction Reaction
The reduction reaction typically takes place in a controlled environment, such as a reactor vessel. The copper salt solution is mixed with the reducing agent under specific conditions of temperature and pressure. The reaction can be represented as follows (using hydrogen as the reducing agent):
Cu2++H2→Cu+2H+\text{Cu}^{2+} + \text{H}_2 \rightarrow \text{Cu} + 2\text{H}^+Cu2++H2→Cu+2H+
During the reaction, copper ions (Cu²⁺) in the solution are reduced to copper metal (Cu), which precipitates out of the solution as fine particles.
4. Precipitation and Filtration
As the reduction reaction progresses, fine copper particles precipitate out of the solution. These particles are then separated from the solution through filtration. The filtration process is critical for removing any remaining impurities and ensuring the purity of the copper powder.
5. Washing and Drying
The filtered copper powder is washed with deionized water to remove any residual reducing agent and by-products. The washing step is crucial for achieving high purity. After washing, the copper powder is dried under controlled conditions to remove any moisture content.
6. Post-Processing
Depending on the intended application, the copper powder may undergo additional post-processing steps such as:
- Milling: To achieve the desired particle size distribution.
- Sintering: To enhance the powder’s properties.
- Coating: To improve the powder’s stability and performance.
Applications of High-Purity Ultra Fine Copper Powder
The ultra-fine copper powder produced through chemical reduction is utilized in a wide range of applications where high purity and precise particle characteristics are essential.
1. Electronics
High-purity copper powder is a key component in the manufacture of conductive inks and pastes used in printed circuit boards (PCBs), semiconductor devices, and other electronic components. The powder’s excellent conductivity and fine particle size make it ideal for these applications.
2. Additive Manufacturing
In additive manufacturing (3D printing), ultra-fine copper powder is used to produce complex metal parts with high precision. The purity and uniformity of the powder are critical for achieving the desired mechanical properties and performance of the printed parts.
3. Catalysis
Copper powder is widely used as a catalyst in various chemical reactions, including hydrogenation and oxidation processes. High-purity copper powder ensures the efficiency and effectiveness of these catalytic reactions.
4. Energy Storage
Ultra-fine copper powder is used in the production of batteries and other energy storage devices. The high conductivity and purity of the copper powder contribute to the performance and longevity of these devices.
Challenges and Considerations
While the chemical reduction process offers numerous advantages, it also presents some challenges and considerations:
- Selection of Reducing Agent: The choice of reducing agent impacts the purity and properties of the final copper powder. Careful consideration must be given to the reactivity, cost, and safety of the reducing agent.
- Control of Reaction Conditions: Precise control